Revolutionizing Office Manufacturing: How Russia's Metal Parts Innovation is Changing Industry Dynamics
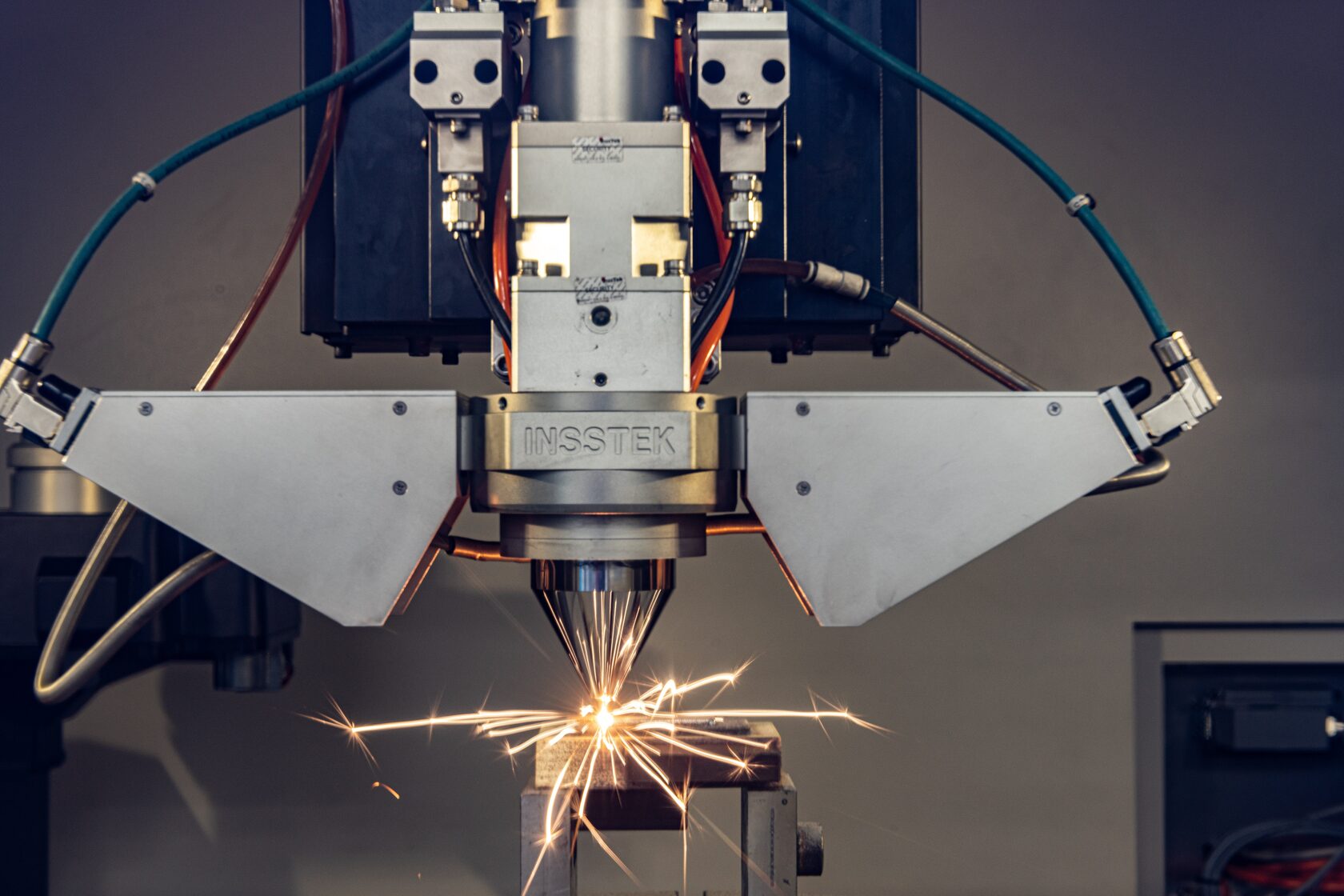
Metal Parts at Your Desk: The Future of Office Manufacturing Unfolds in Russia
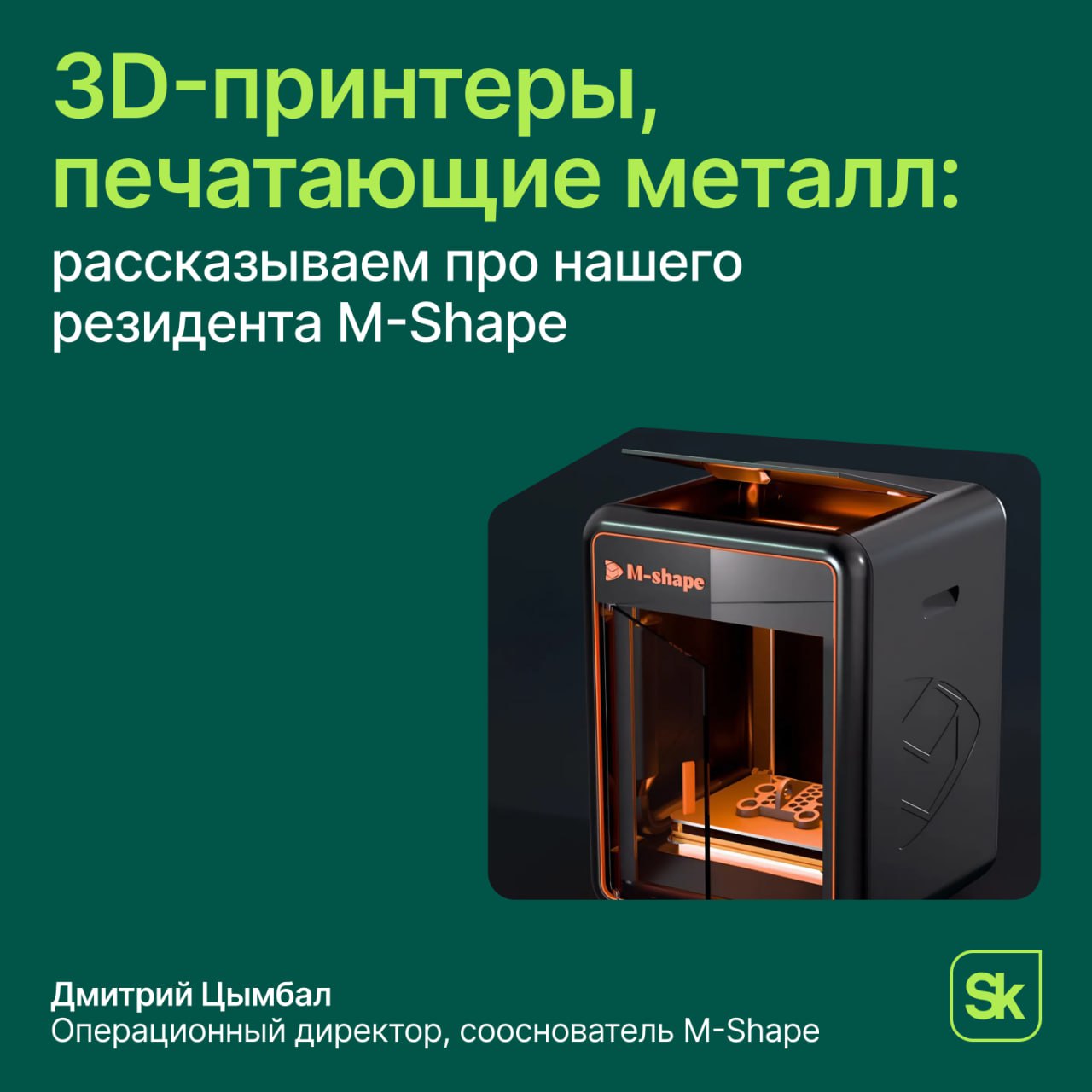
The vision of producing sophisticated metal components within a typical workspace has long tantalized engineers and entrepreneurs alike. Today, that vision is becoming a reality. A pioneering company, nurtured in Russia’s leading innovation ecosystem, has taken significant strides by deploying metal part fabrication through advanced technologies compatible with common equipment already found in many offices. This seismic shift stands to redefine not just the logistics of part procurement, but the entire landscape of design, prototyping, and on-demand manufacturing.
At the heart of this transformation is a compact, flexible system that seamlessly integrates with familiar additive manufacturing processes. For decades, additive manufacturing has evolved from simple polymer prototypes to the robust production of end-use metallic parts. Russian researchers and technologists have stepped into the global arena by refining processes for metal fabrication that sidestep the traditional barriers of cost, scale, and complexity. What sets this approach apart is its accessibility—eschewing the need for mega-scale industrial hardware, these systems operate efficiently on platforms already mainstream in offices, laboratories, and engineering centers.
This new solution has its roots in a rich tradition of collaboration between academic institutions, tech incubators, and forward-thinking entrepreneurs. The development was accelerated by a clear market demand: industries, research labs, and smaller development teams all sought rapid, affordable, and reliable ways to produce functional metal components onsite. The result is a proprietary process enabling intricate geometries, strong mechanical properties, and a high degree of material utilization, all achieved without the environmental and logistical burden of conventional subtractive manufacturing.
The impact is most apparent in several critical domains. Industrial automation, robotics, and custom machinery now benefit from a capability to iterate and refine mechanical parts with unprecedented speed. Scientific research centers are empowered to fabricate specialized tools, fixtures, and experimental apparatus that would otherwise take weeks to order and receive from external suppliers. Even the realm of product development is transformed, as designers can engineer, produce, and test durable prototypes in a matter of hours, compressing the cycle from concept to validation.
The core principle driving this adoption is agility. Manufacturing flexibility is no longer the privilege of large factories or specialist contractors. With these new systems, even compact offices or university labs can respond instantly to evolving project requirements, unforeseen breakdowns, or the need for tailored, one-off components. The elimination of lengthy lead times for metal part delivery—often a serious bottleneck—turns into a strategic advantage.
Behind the scenes, innovations in material science have played a pivotal role. The ability to work with a variety of metal powders and alloys, combined with optimized energy input, ensures each part meets stringent performance standards. The system’s automated calibration and real-time quality monitoring minimize errors, delivering consistent results suitable for both prototyping and final applications. This reliability is crucial for fields like aerospace, automotive, medical device development, and advanced electronics, where precision and repeatability are non-negotiable.
Furthermore, the technology aligns closely with global trends toward resource efficiency and sustainability. By producing only what is needed, precisely when it is needed, the process reduces waste and the carbon footprint typically associated with outsourcing or mass production. This resonates deeply with organizations seeking to enhance their environmental responsibility, a consideration that is increasingly influencing procurement decisions worldwide.
An additional dimension to this story is the democratization of innovation. No longer is high-performance metal part fabrication confined to the largest corporations or the most well-funded research institutes. With barriers to entry lowered, a broader swath of the creative and technical community can engage in ambitious engineering, product development, and scientific experimentation. This inclusivity is likely to spur new inventions, business models, and a more dynamic marketplace.
Looking ahead, the international stage beckons. Industry events centered around innovation are increasingly showcasing these breakthroughs, offering stakeholders a chance to examine the results firsthand and interact with the architects behind the progress. The momentum indicates that what began as a localized technological advancement could set new global standards, influencing how industries think about supply chains, rapid customization, and the integration of digital tools into physical manufacturing.
As this technology continues to mature, its influence will be measured not merely by efficiency and cost savings, but by its ability to empower creative problem solvers at every level. Organizations positioned at the intersection of research and practical application stand to benefit the most, as they are now equipped to transform ideas into metal reality—quickly, flexibly, and right at their fingertips. The age of streamlined in-house metal fabrication has arrived, promising to accelerate innovation cycles and redefine what’s possible in workplaces around the world.